CPPRI: Paper Industry contributes Rs. 8000 Crores to the National exchequer with a turnover of Rs.70000 Crores
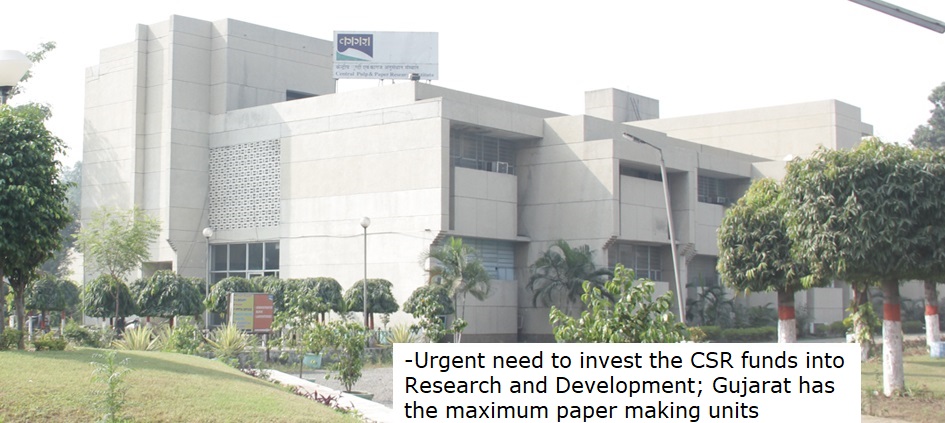
CPPRI: Paper Industry contributes Rs. 8000 Crores to the National exchequer with a turnover of Rs.70000 Crores
- The proposal for leasing of degraded forest lands for pulpwood plantations needs to be fast tracked by the Ministry of Environment, Forests and Climate Change (MoEF&CC).
- Urgent need to invest the CSR funds into Research and Development; Gujarat has the maximum paper making units
- The total operating installed capacity in the sector is 23.99 million tons per annum and the production is 21.36 million tons per annum.
-
2022 | The Pulp and Paper Times :
The annual report of Central Pulp & Paper Research Institute for FY 20-21, reveals that the year 2020-21 will be remembered as historical year of fight against pandemic Covid19. Indian Pulp and Paper Industry has also faced a number of challenges due to Covid 19. Central Pulp and Paper Research Institute returned swiftly to its normal working from June 2020, after the lockdown period of March 24th to till 31st May 2020.
In the area of product development CPPRI has been consistently working and has successfully completed two different projects for production of fluff pulp from bamboo and production of high purity dissolving pulp from bamboo and whole jute. In addition to this consultancy was provided to a number of startups companies for utilization of cellulosic biomass for production of pulp for table wares or paper crockery.
PRESENT SCENARIO:
Indian paper industry is one of the most fragmented sector with production capacity ranging from 5 TPD to 1650 TPD and geographically highly dispersed. During the decade 2010 to 2020 Indian Paper Industry registered a substantial growth which resulted in a two fold increase in production from 10.99 Million Tons (2010) to 21.36 Million Tons (2020).
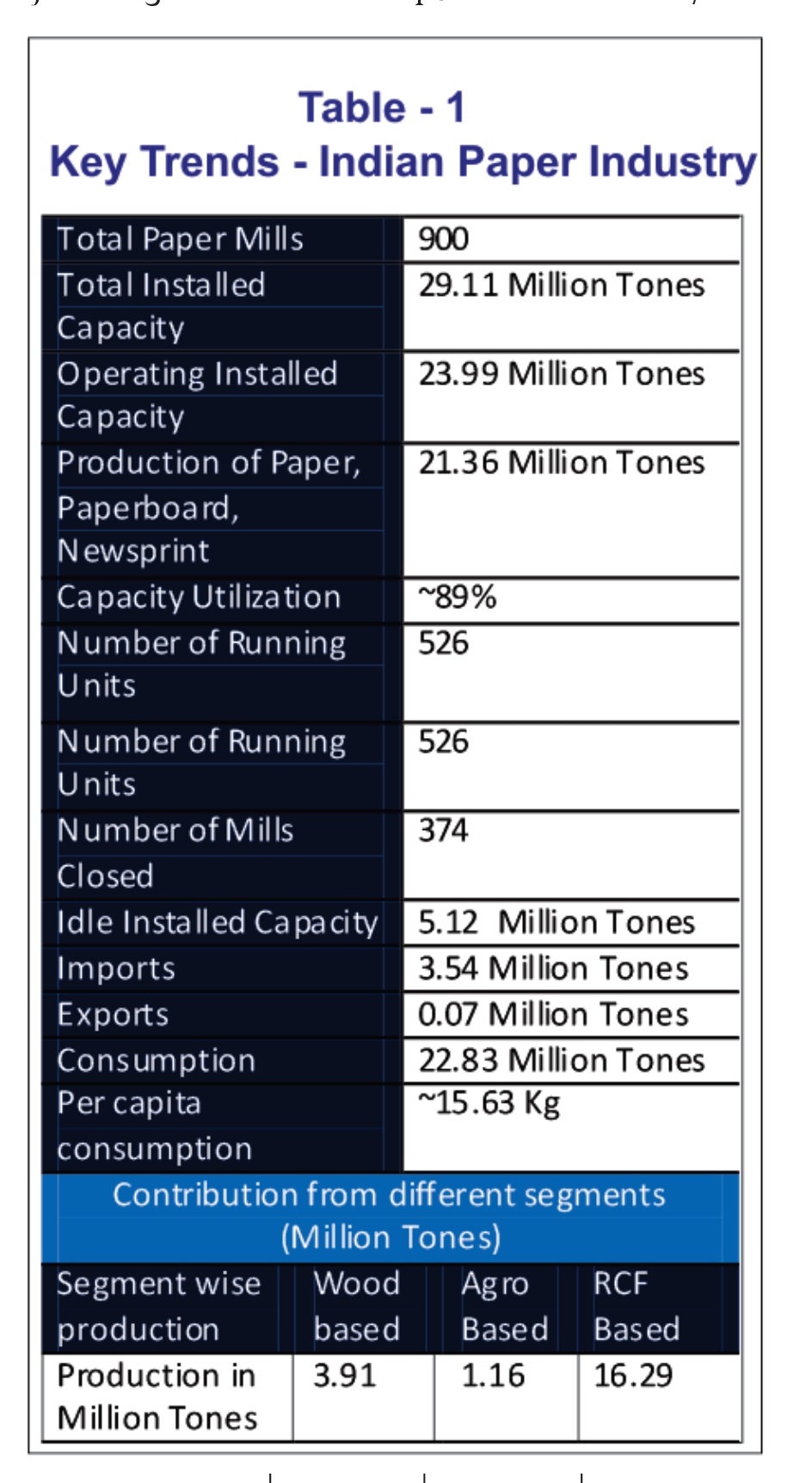
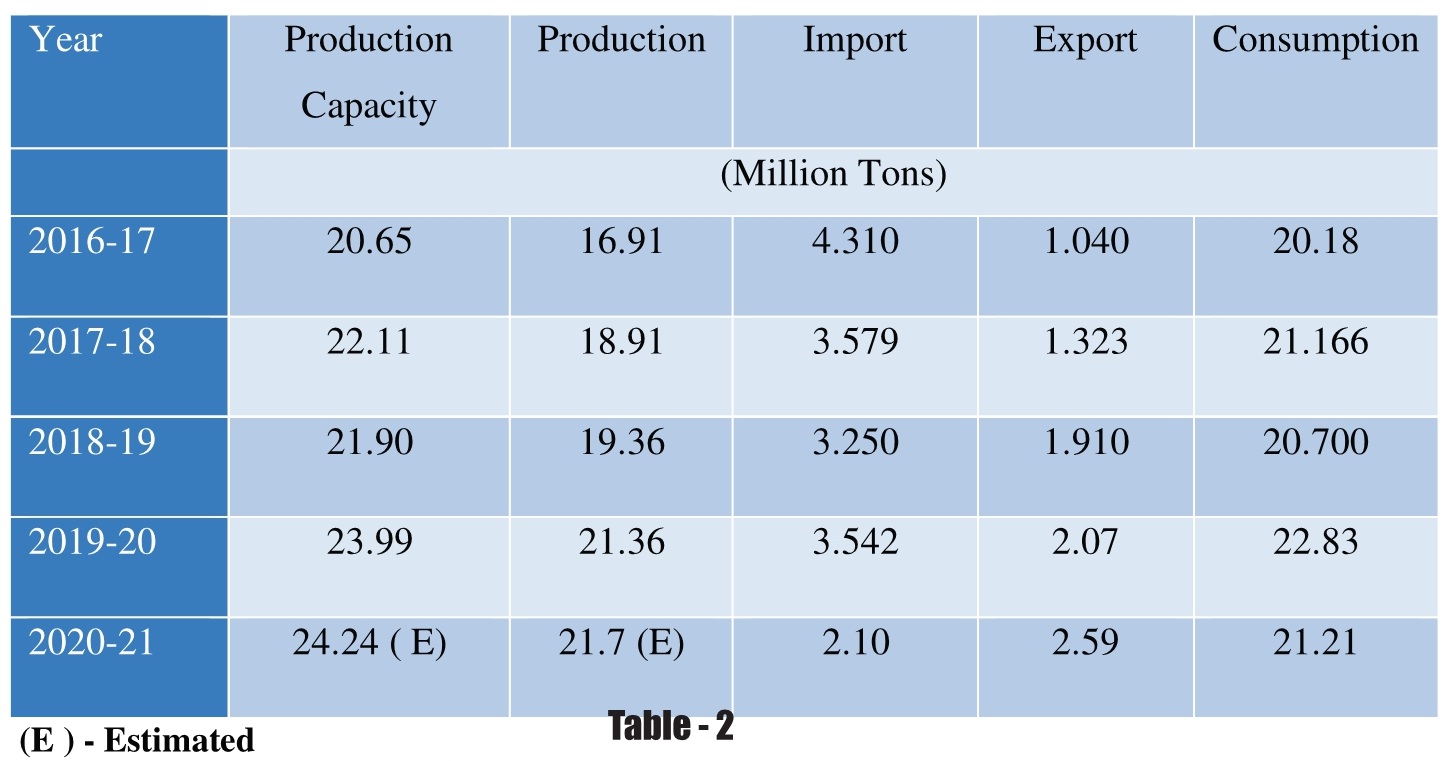
This growth story of Indian Paper Industry has been hampered due to the pandemic situation. Every sector of the industry was forced to stop operations due to nation wise lockdown imposed after March 2020. Initially, Indian Paper Industry also shutdown the operation but after few weeks, paper sector was recognized as an essential service in many states and was allowed to operate with strict COVID Norms.
Upon resumption of operations, strong demand of pharmaceutical sector, FMCG sector, online shopping, and increase use of hygienic paper products etc., gave the momentum to the packaging segment. But, on the other side, due to closure of professional premises, academia, institutions, etc., the demand for writing and printing paper.
In the fourth Quarter of 2019-20 most of the well known paper units reported downfall in the turnover figures.
In FY 2020-21, mills were forced to close down on an average of 50 days and as a result most of the mills did not file performance report and are still doing compilation of turnover and production figures. In the mid of 2020, industry was facing immense shortage of raw material mainly because of logistics interruption, shortage of containers, labor issues, etc,. After June 2020, all units resumed their process with 60% to 70 % capacity utilization. However, due to ongoing demand of pharma and FMCG sector the packaging sector did not loose its pace and registered almost same production levels as that exhibited in 2018-19.
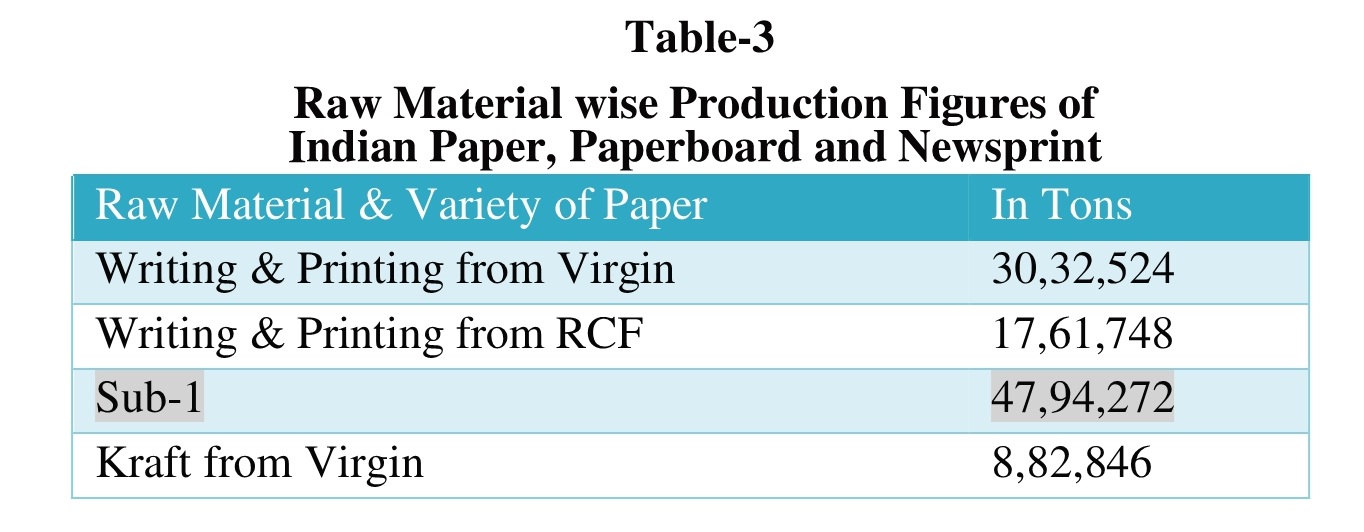
Strong demand of packaging grade paper provided support to the industry and therefore, 71% production share of market remained largely unaffected by the pandemic impact. Further, some green field as well as brown field projects also started their commercial production of packaging grade paper, which covered up the loss of production wiped out the loss of production figures of the writing and printing sector.
Today there are about 900 paper mills spread across the country. The total operating installed capacity in the sector is 23.99 million tons per annum and the production is 21.36 million tons per annum. Table -1, presents a snapshot of the Indian paper sector. Nationally, paper sector is one of the core entities in terms of providing employment in the Indian hinterland. Overall, 2.5 million persons are directly and indirectly getting their livelihood from this sector.
At the national level, this sector contributes Rs. 8000 Crores to the National exchequer with a turnover of Rs. 70000 Crores. Fueled by the National Priority of a knowledge-based economy, the sector is likely to emerge as a significant contributor to the Government's target of achieving an overall growth of 8% in manufacturing.
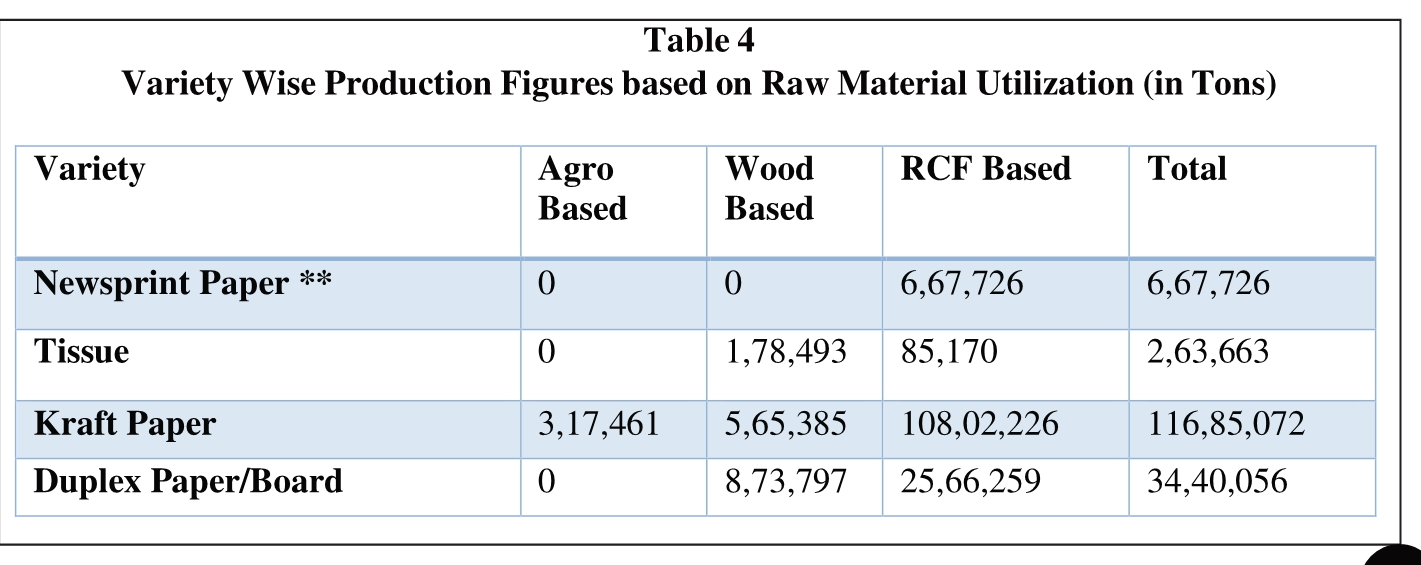
A STATISTICAL BACKGROUND NOTE ON INDIAN PAPER INDUSTRY:
The consumption of paper in India increased from 16.91 million tons in 2016-17 to 22.83 million tons in 2019-20. During this period India's paper consumption registered CAGR of 6% compared to the global growth of 3% making India one of the largest growing paper markets in the world. Relevant figures are placed in Table 2.
Paper industry has three broad categories of products i.e. Writing & Printing Paper, Packaging Grade paper (Kraft paper, duplex paper, board and paperboard) and Newsprint. Table 4 gives the category wise production figures. As can be seen, the newsprint sector continued to be affected by the low cost imports, thereby this sector clocks the production figure higher only to Tissue Paper segment. Further, all the production of Newsprint is coming from the waste paper based mills. Production of writing and printing paper gets contribution from the mills using all the three type of raw materials.
In spite of sufficient domestic capacity of packaging grades paper manufactures, imports under HS code 4804 & 4805 are taking place in India. Industry sources ascribe these imports to the zero to zero tariff regimens under various free trade agreements.
In 2020-21, steep hike can be seen as nationwide lockdown affected the local production and where for, to fulfill the domestic demand almost double imports were recorded in the month of April & May, 2020-21. But, as industry resumed its operations, dependency on the imported kraft paper reduced to pre-covid level.
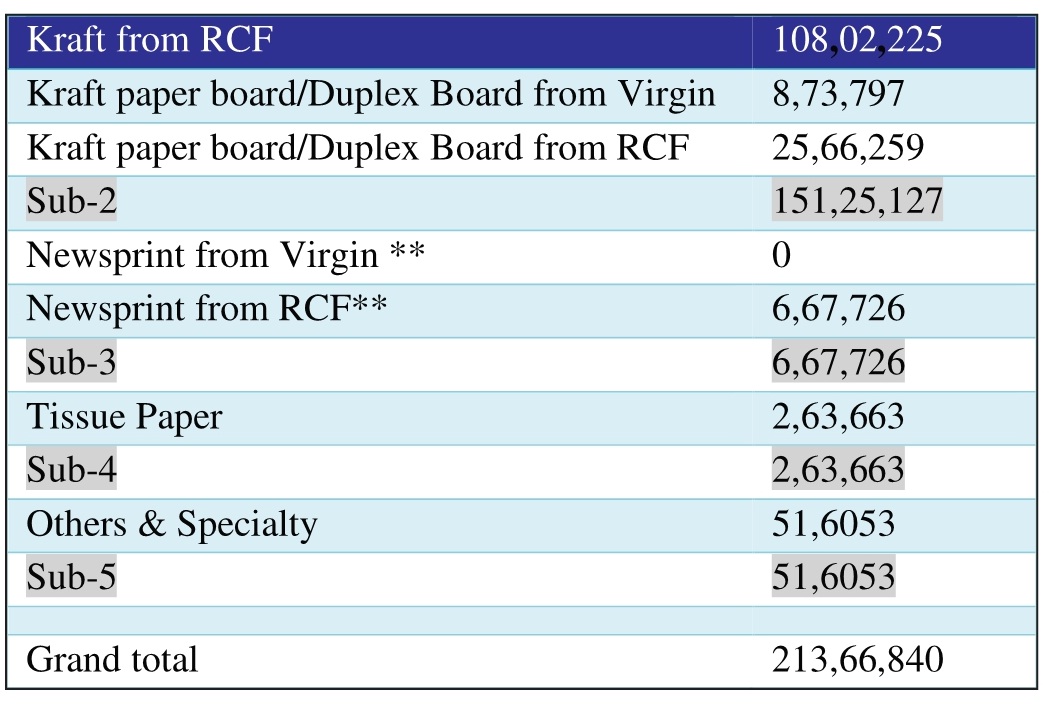
If the numbers alone are considered, then Gujarat has the maximum paper making units. However, most of these units are recycle fibre based. The state of UP has the second largest number of paper mills. Most of these are in the Muzaffarnagar and Meerut clusters. Most of the major players are in Tamilnadu, Andhra Pradesh and Maharashtra. The major pulp and paper mills clusters are in and around Muzaffarnagar, Vapi, Muzaffarnagar, Kashipur, Coimbatore, and Ahmedabad.
Major achievements of CPPRI during 2020-21:
Production of Fluff Pulp from Jamaica Bamboo
Cellulosic fibre (pulp) is the raw material for a number of end products. One of them is hygiene products like adults and baby diapers and sanitary napkins. Conversion of cellulosic pulp for production of super absorbent fluff material to utilize in diapers and sanitary napkins is not only a substantial value addition but also an environment friendly solution too. Cellulosic pulp helps in reduction of synthetic super absorbent material used in these products. The process has two steps:
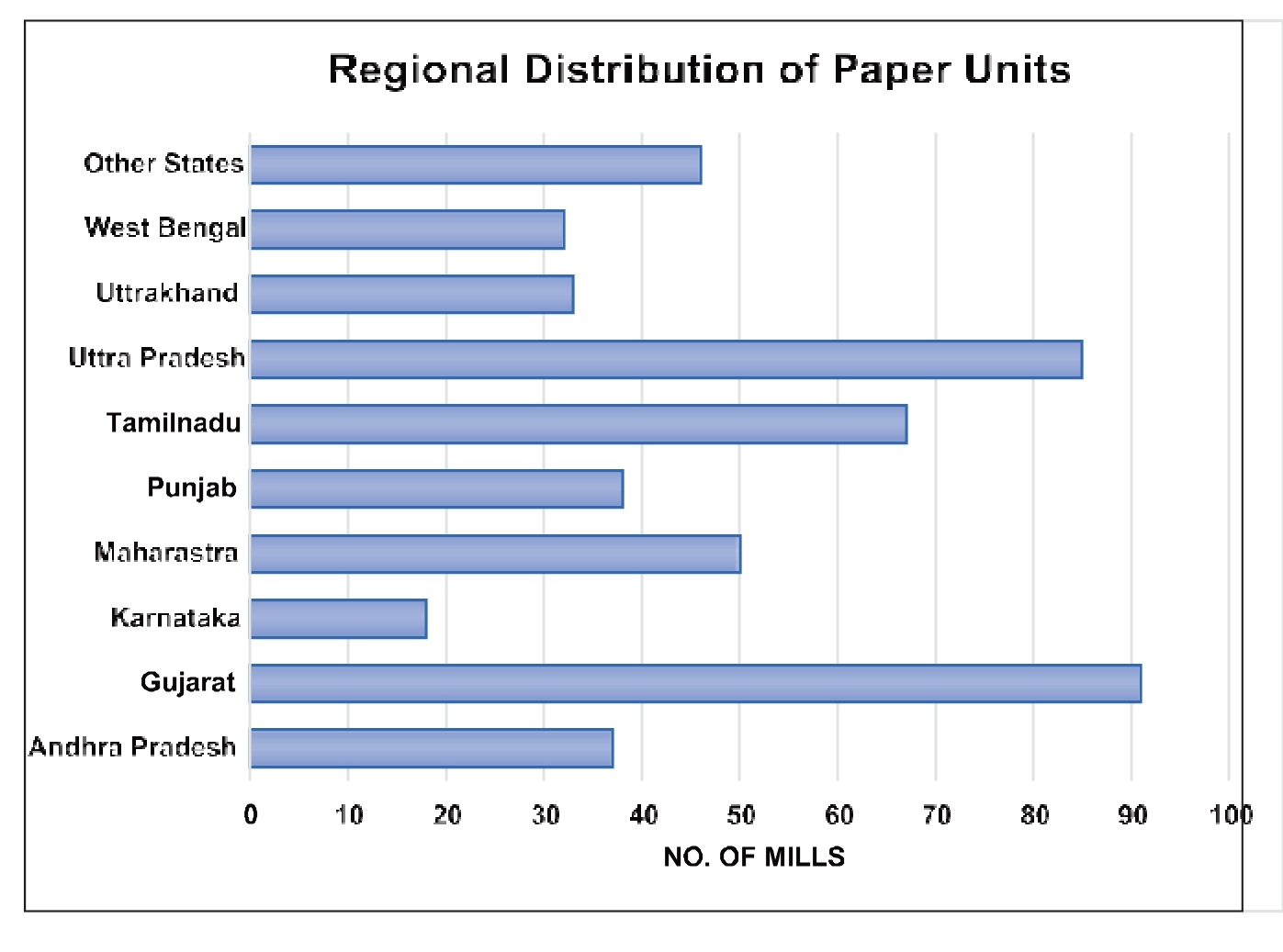
- Kraft pulping of bamboo and TCF bleaching of optimization of unbleached pulp.
- Hammering of TCF bleached bamboo pulp into fluff.
The fluff prepared from bleached kraft pulp of bamboo is comparable to the pulp available in market. The project has open the possibility to explore other long fibre raw materials like jute, banana etc to utilize in production of fluff pulp.
Production of Dissolving Grade pulp from Bamboo and whole jute
The fibrous raw material has not only one end use i.e. pulp and paper. Basically pulp is the cellulosic source of raw material for many other end products. Higher the purity of cellulose after pulping and bleaching, higher will be value addition which may turn into better economic viability.
Government of India aims to support the farmers, the growers of the crops like whole jute, bamboo.
National Jute Board has sponsored a project on production of high purity dissolving grade pulp from whole jute and bamboo. Whole jute has higher silica and initially it took numbers of experimental trial to remove silica from pulp in different process stages viz. pre-hydrolysis, pulping and bleaching. After sustained efforts we succeeded to produce bleached pulp with +94% alpha cellulose and all other characteristics in the desired accepted range dissolving grade pulp. The trial of conversion of pulp to viscose and to fibre was carried out successfully at Aditya Birla Science and Technology Co. Ltd., Mumbai, Maharashtra. Further work is in progress on feasibility and pre pilot scale trials.
CONCLUSION
The Indian paper sector has performed fairly well over the years even though it was confronted with factors internal to the sector as well as due to externalities. The sector has unutilized capacity primarily due to acute fiber shortage in the country. Another reason for low capacity utilization has been the ever-increasing input costs particularly for energy inputs (both coal and non-coal).
The sector is very capital intensive –the ROI in its case is five to seven years. This fact has been reflected over the decades that almost all capacity addition have occurred largely through brownfield expansions. Further, most of these expansions have been in the waste paper based segment and due to de-bottlenecking measures taken by individual units, as low investment options.
Even in the above scenario, the Indian paper sector has taken notable steps to maintain smooth operations and remain competitive to the maximum extent possible in the post globalization era. The work carried out in raw material augmentation and its utilization by the sector is very commendable. Nearly all wood-based paper mills have robust plantations programs in place wherein they can source the major volumes of the required raw material. The agro based segment has mastered the art of paper making from what are known as short fiber and inferior raw material. India is one of the few countries that produce writing/printing paper from bagasse and other agro residues.
Time is now ripe for the Industry to look beyond the medium term and invest in R&D for long term sustainability. There is an urgent need to invest the CSR funds into R&D which not only help the sector but also will impact the communities that are directly or indirectly involved with the paper sector.
There is a pressing need to ensure a sustained availability of quality lignocellulosic raw material for paper making in the country. In this reference the proposal for leasing of degraded forest lands for pulpwood plantations needs to be fast tracked by the Ministry of Environment, Forests and Climate Change (MoEF&CC). If the industry is assured of availability of quality raw material well into the future, it can plan investments and expansions with a long-term vision.
Also, urgent interventions are needed for revising the ITC-HS codes for paper (Chapter 48) at the eight-figure level in order to reflect the needs of the current trade of paper in India. This is needed to reduce the increasing imports of these items under the “Others” category. Also, certain varieties such as copier paper needs to be given a specific code under Chapter 48.
Energy is clearly the most important parameter that needs to be monitored after the raw material availability. The industry needs to shift to energy efficient technologies, but it needs funds for the same which are difficult to be available on commercial terms in view of the long ROI. Whereas the Bureau of Energy Efficiency has made some efforts to help the industry move towards energy efficiency under PAT -2 and the National Motor Replacement Program (NMRP) through its subsidiary, Energy Efficiency Services Ltd. ( (EESL), direct funding may have to be planned for inducting energy efficient unit operations in the pulp and paper sector.
Currently, the paper sector is moving towards an era of new opportunities driven by introduction of biorefinery approach and possible ban on Single Use Plastic. These opportunities will open new avenues for utilization of all possible unique products from the constituents of ligno-cellulosic raw materials produced in a biorefinery. This would have the potential to change the face of the Industry. The sector may well look into the future where pulp and paper would actually be the by-product of the biorefinery operations, and the other value-added eco-friendly products will become the main stream products contributing substantially to the bottom line.
About CPPRI:
Central Pulp & Paper Research Institute, a National level Institute was established in 1980 as an autonomous body under the administrative control of Department of Industrial Policy & Promotion, Ministry of Commerce and Industry, Govt. of India to promote R&D in the field of pulp & paper. The origin of CPPRI dates back to the year 1975 when the UNDP-GOI Project became operational. After the conclusion of the UNDP Project, the facilities thus created were utilized to fulfill the long felt need for R&D needs of Indian Pulp and Paper Industry. Thus after the approval of the Cabinet, Central Pulp & Paper Research Institute (CPPRI) came into existence in November 1980. Existing R&D facilities were continuously upgraded with the aid of Plan Funds received from the Government of India.
Web Title: CPPRI Paper Industry contributes Rs 8000 Crores to the National exchequer with a turnover of Rs 70000 Crores