Design Of Drilled Press Rolls Cover in Paper Making Application
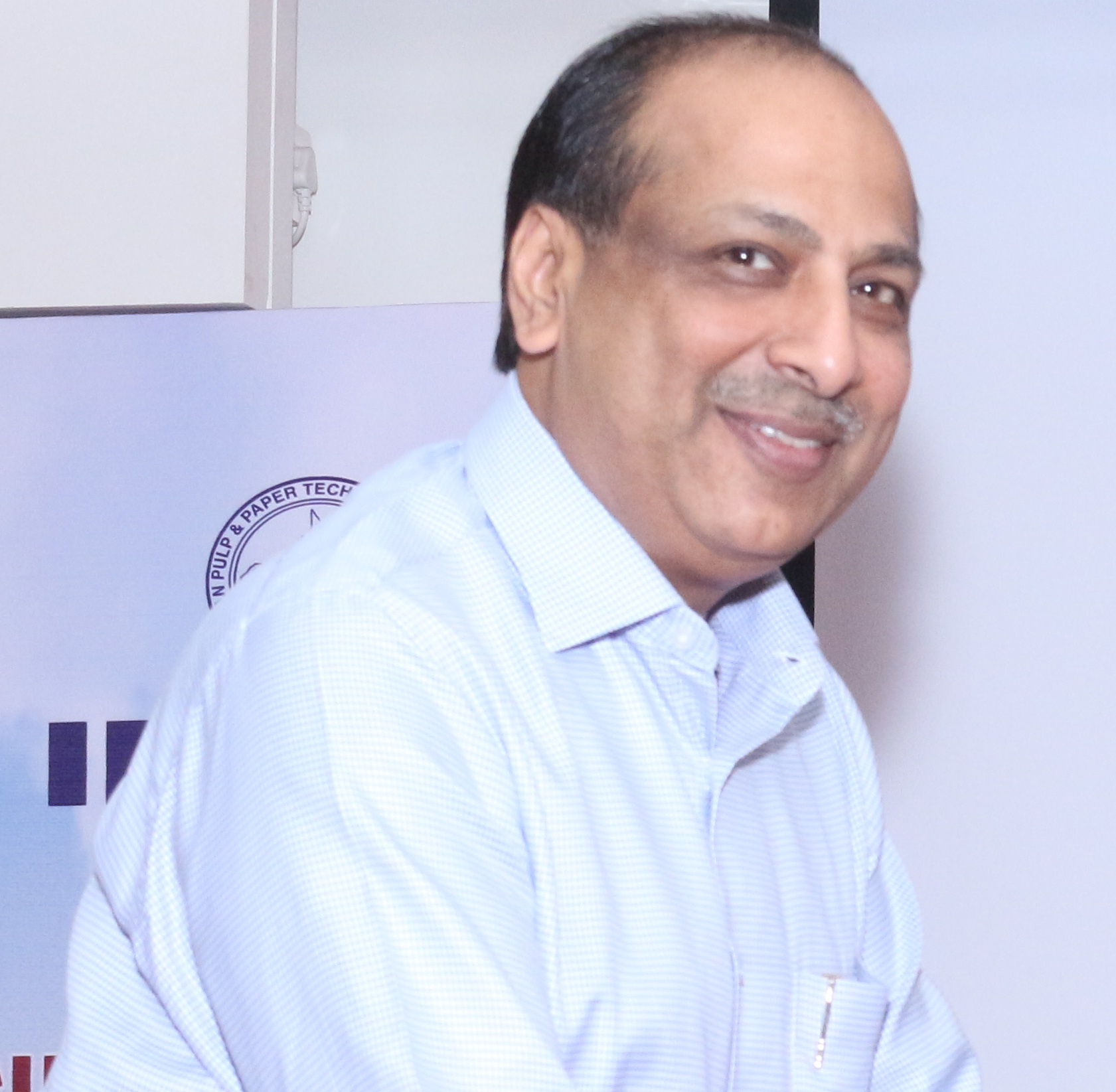
Design Of Drilled Press Roll Cover in Paper Making Application
Determining how the web gets formed and compacted from forming section to press section appears to be a fairly simple task. However, lot of factor must be taken into consideration if the process has to minimize problems and if the result of the processing has to be the best possible.
The paper web formed in the forming section passes onto the press section and this is followed by the pressing of the web on the paper machine through the nip of two rolls running under pressure. This effect of pressure in nip between the two rolls further removes the water, thus improving the compactness and strength. The pressing operation is critical and important as it relates to the economics of a paper machine and accordingly determines the dryness of the sheet entering the dryer section.
Now, to be more precise the design and the number of nips are most important to critically define a press section. It should be noted in this context that maximum removal of water in forming and press section is more economical, then to remove it in dryer section. Making the press design should be more stressed for:
-Graduation of dryness in nip.
-Less no. of nip with highest possible dryness has to be achieved.
-Unnecessary fibre crush or distortion should be avoided, as it affects the paper quality.
-Rigidity of press structure and press rolls enhances the run ability of paper in press section.
-And of course, the fabric handling easiness is to be ensured.
Technicians and paper makers claim to achieve a dryness level of 36-55% in this Press Section, which categorically is governed by the above detailed parameters.
Moving on the subject, a better and optimum roll cover of a press section should be: Resistant, Durable, Efficient and Economical.
Amar Elastomers over the study of several years has computed the Blind Drilled Press Roll Cover, nomenclature as “DWELL PRESS†, which had been significantly designed, keeping almost the entire design parameters.
-The overall hardness uniformity of the cover results to better wear stability at higher nip pressure. This results to uniform and maintains more efficient nip pressure throughout the nip width and in the cross directional length of the roll.
-Programmed drilling pattern (diameter and pitch) helps paper makers for optimal quality of paper. Basically the nip pressure to be applied on what grade of paper makes our technician to get this pattern programmed for the Press Section.
-Next comes the uniformity in the de-watering i.e. the cross directional dryness/moisture profile, which is thus maintained as a result of uniform hardness and the drill pattern.
-Selection and maintaining the thickness of the rubber cover, also improves the dynamic stability of the cover.
-In recent days the edge crack on the drilled rolls has raised as a major problem and tremendously reduced the overall life and performance of the roll covers. A recent study done by us on number of high speed machines and higher nip loaded Press Section has made it clear that proper edge relief and end dub is more important and critical to avoid end cracking of drilled rolls. The combination of the selection of rubber cover thickness and the edge relief/end dub constitute to a good programmed cover, resulting to prolonged life of the cover. We had tried to follow the studies done by the experts and technicians in the past by keeping the edge relief in the range of 1.5 to 2% of the total face length and surprisingly it resulted good as on higher rubber displacements, the rubber cover gets better margin to get accommodated for a uniform nip profile.
Result show that a betterment in the reduction in sheet moisture in a level of 2-4% has been observed, which of course is a big energy saving as compared to get it done in drying section. As a result of higher dryness achievement, the productivity increases.
Keeping the designed parameters in consideration and even nip profile helps to avoid paper crushing in the nip.
To summarize, rubber cover design management using the tools of hardness, drill pattern, thickness of cover, compound material and edge relief, optimize the performance of a drilled rubber covered roll. Correct choice of press design and rolls, use of supplier expertise and most important, understanding of the theory can make significant contributions to both production efficiency.
Note: The contents submitted by Mr. R.K.Agarwal, This paper is related to studies and observations done on various paper machines during his carrier in Amar Elastomers as a manufacturer of rubber covered rolls for the last eighteen years.
Web Title: Design Of Drilled Press Rolls Cover in Paper Making Application