Fiber Recovery And Water Reuse in Paper Mills Through Closed Water Loop- A need of hour
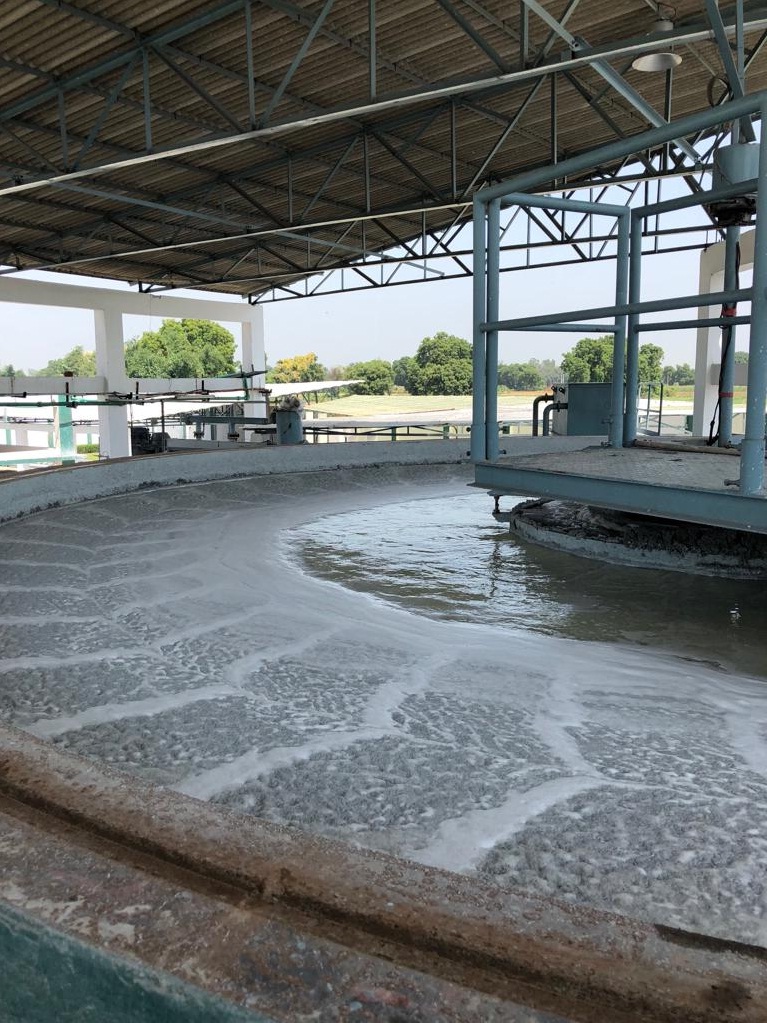
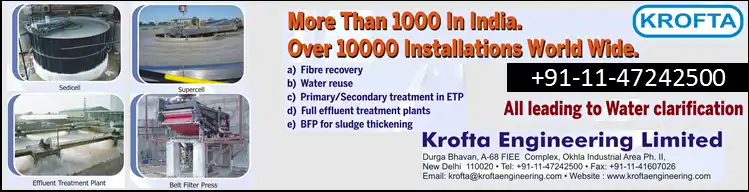
Fiber Recovery And Water Reuse in Paper Mills Through Closed Water Loop - A need of Hour
The Closed Water Loop for mills based on waste paper in India and abroad where mills are easily implementing the same and save the environment from pollution and save energy and water resources depleting in the earth’s stata.
Since the paper industry is a high water consuming industry
- in 1970s the water consumption was 400 m3/tonne of paper
- in 1980 the consumption came down to 250 m3/tonne of paper
- in 1990 the consumption came down to 100 m3/tonne of paper
- in 2000 the consumption has came down to 50 m3/tonne of paper
- in 21st century the efforts are being made to make it 2m3/ton of paper
But the consumption of this water still has a very higher side compared to the mills operating in Europe and other Middle east countries. The technology is based on clarification of suspended solids through our patented equipment SEDICELL which operates on the principle of Dissolved Air Flotation System and have 30 minutes retention time and can recover fiber by flotation and fillers and fines by sedimentation. The quality of the fiber recovered is excellent, which can be reused in case of Kraft/ Duplex/ Writing Printing paper mills if our Sedicell is installed as a primary clarifier. The clarified water from the Sedicell is taken into a holding tank, where it can pass through pressure sand filter and activated carbon filter with a pump of 30 meter head which is designed as per the flow and then the clarified water from the activated carbon filter is collected in a holding tank and reused back in the plant and paper machine showers.

APPLICATIONS OF SEDICELL
1. MACHINE BACK WATER FIBER RECOVERY
It recovers fiber on the top by flocculating and collecting at the top of the Sedicell with the help of a scoop which collects the fiber and transport to the collecting tanks. The filer material which is added as soap stone or calcium carbonate in Paper making processes settles down in the bottom a scrapper which is running continuously alongwith the scoop collects the filler material in a tank which can be reused again in the paper making process saving soap stone, filler as well as fiber. The clarity of the water recovered varies with the usage of chemicals used as flocculant to recover the fiber. The achieved clarity of this clarified water is upto 20 – 100 ppm in various mills. The clarified water when used in the pulp mill has an advantage over the other processes being used for recovery of the fiber increases the brightness of the pulp being manufactured. The fiber recovered can either be reused in our paper making process or can be squeezed on a belt filter press from 2 – 25% consistency can be used either by board mills or any other inferior quality of the paper wherever it is applicable.

2. IN THE DIP PROCESS
Sedicell is widely used in deinking plants also where the entire effluent is taken and clarified in the Sedicell. The sludge recovered on the top is not at all used in the paper mills because it contains black ink particles and some foreign materials which are separated during deinking process. It is recommended, the belt filter press for squeezing this sludge recovered from the Sedicell and the clarified water having suspended solids of less than 50 ppm should be passed through the pressure sand filter (PSF) and activated carbon filter (ACF) to remove the porous material and partial colour. The clarified water after this process can be reused again in the pulp mill without wasting a single drop of water and also for agro pulping based paper machines.


3. RETROFIT OF CLARIFIER – HIGH HYDRAULIC LOADING
Sedicell has replaced the primary and secondary clarifiers in the effluent treatment plant saving huge civil construction costs and space with paper quality of effluent being clarified with this equipment. The efficiency of this equipment is 96% as compared to a conventional clarifier which is 70 – 80%. The COD reduction in the Sedicell is 35 – 40% because it operates on the principle of Dissolved air flotation system which percolates air in dissolved form in the clarified water and 25% of which is reused again for flocculation of aerator effluent. The dissolved air helps in floating the fibers on the top with the help of flocculants.

Example : for a flow of 6000 m3/day flow, the conventional clarifier will have dia 18 M and Sedicell will have dia of 8 Meters. More details can be provided on case to case basis.

The furnish of the aeration tank is also improved because of the efficient removal of suspended solids from the raw effluent. The suspended solids in this case of clarifier can be reused in case of kraft and duplex paper mills but in case of writing printing papers it has to be disposed off to the users or burned in the boiler.
The purpose of providing filters after Sedicell is to reduce the suspended solids to less than 20 ppm through KS Filter and PSF but in Spray Filter, we get clarity less than 50 microns where the clarified water from the Spray Filter can easily be reused in the paper machine showers by replacing fresh waters.
The balance effluent flow ranging between 10 to 20% is treated through effluent treatment plant based on aerobic process and again passed through Pressure Sand Filter and Activated Carbon Filter to reduce the suspended solids less than 50 ppm, BOD less than 30, COD less than 150. These parameters are required to be maintained by effluent treatment plant running religiously to achieve the parameters so that this water can be disposed as per pollution norms and environmentally handled as per each Country’s norms.
About the technology developer:
Krofta India was started in 1983 as a joint venture collaboration with Dr Milos Krofta. He was the founder of Krofta globally and developer of the Dissolved Air Flotation Technology. We offer proven designs by incorporating DAF (Dissolved Air Flotation Technology) to handle waste water treatment systems for industrial as well as municipal applications.
For paper machine showers water clarification, Krofta Engineering has developed following types of filters such as Spray Filter, KS Filter, Pressure Sand Filter, Activated Carbon Filter.
Krofta Engineering Limited is involved in many projects in giving the Closed Water Loop in India, UAE, Bangladesh, Vietnam, Iran, Pakistan, Sri Lanka, Nepal etc.
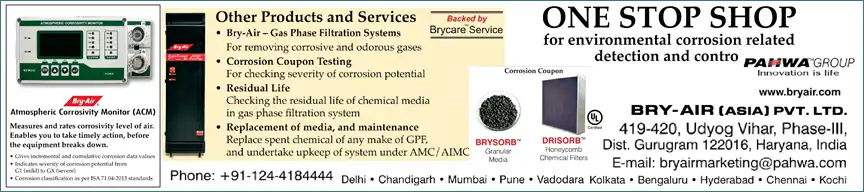
Web Title: Fiber Recovery And Water Reuse in Paper Mills Through Closed Water Loop A need of hour