IBL has the credit to successfully utilise difficult Bio mass on commercial scale like Rice straw (Parali), Mustard straw and other waste
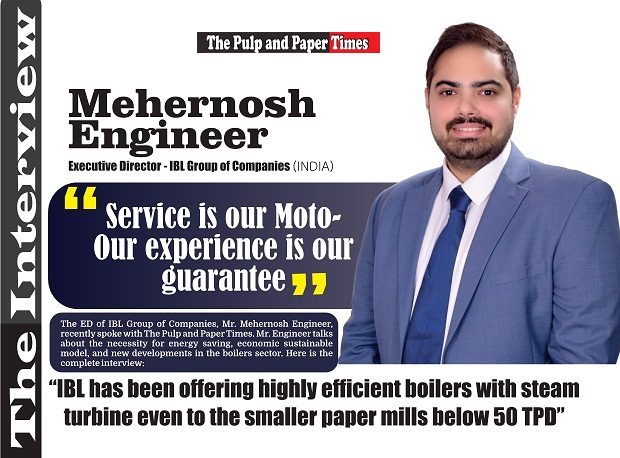
IBL has the credit to successfully utilise difficult Bio mass on commercial scale like Rice straw (Parali), Mustard straw and other waste
Service is our Moto- Our exprience is our guarantee
The ED of IBL group of companies, Mr. Mehernosh Engineer, recently spoke with The Pulp and Paper Times. Mr Engineer talks about the necessity for energy saving, economic sustainable model, and new developments in the boilers sector. Here is the complete interview:
The Pulp and Paper Times | 2022:
Q: Please give us a small introduction of Industrial Boiler Limited (IBL)
In 1974, Industrial Boilers started boiler manufacturing in Vapi, Gujarat. The company took off in 1978 with the manufacture of Vertical Cross Tube Boilers which were fully riveted. A hundred boilers later, Package Boilers of welded design were produced. In 1986, Industrial Boilers launched commercial Fluidised Bed Boilers (FBC) and with the advent of this technology, the company reached new heights with advanced models being launched at regular intervals.
Today The IBL Group is now a Research driven, industrial organisation specialising in Design and Manufacturer of Process Steam Boilers, Industrial Boilers, Power Boilers, Turbines, Pressure Reducing Steam turbines,Mini Power Plants, Specialised Combustion solutions, Autoclaves and Vulcanisers, Solar Thermal Systems, ESP, Bag Filters and Pollution Control Equipments.
With a vast pool of highly talented and experienced engineers, IBL has continued to maintain its reputation as a Research Powerhouse of Boilers.
With Boiler technology flowing thru our veins, IBL is the international market leader in the field of Biomass Boilers and at the cutting edge of technology.
Our research is 5 to 10 years ahead of time so that we can foresee developments and provide absolutely latest technology to our customers. Our rich history coupled with innovation is our strength - a formula that always works.
Service is our Moto – Our exprience is our guarantee
Q: In simple words, what is the role of a boiler in process industries like paper? and how it is important. How can a boiler from IBL improve the efficiency of paper mill production?
Today the fuel cost of fuel is a most important fraction in the cost of paper production. For example, for manufacturing Kraft Paper from Imported Coal the fuel cost in the total cost of paper is around 10 to 19%. Also the cost of power is also around 15 to 20% in the total cost of kraftpaper. Looking to the above the boiler efficiency is the most important factor along with Cogeneration of power. Normally in a 100 TPD kraft paper plant 50 to 75% power can be generated through co-generation. Also the use of Biomass and the installation of Multifuel boiler will greatly benefit the paper industry so that they can utilise cheaper biomass as available in different season locally.
Q: Government is committed to replace the traditional input fuels used in the industrial boilers by PNG (Gas). How IBL is ready to meet the requirement of PNG compatible boilers? It is possible to convert the existing boilers (Coal based, FO Fired or Straw based, and others) into PNG-compatible boilers?
In the past PNG was being actively promoted as an environmentally friendly fuel. But the present cost is high and availability is certain areas is a big question mark. Bio mass as a fuel would be better than PNG as it is carbon natural and a renewable source of energy. Also the government is favouring the farmers to encourage farming which is almost doubling their production so definitely bio mass usage is being encourage in India.
Q: Water is a vital element in steam generation. There is a variety of ground and surface water available across India which requires pre-treatment before feeding to the boiler. In this case, do you provide any kind of customization in the boiler, training which makes operation optimized according to the nature of input water?
We at the IBL group regularly arrange for boiler engineer and operator training programs. In these programs all aspects of safe operation, fuel efficiency, environment obligations and water treatment beside other points are imparted.
Q: What global trends do you see in the context of energy generation? As the paper industry is a high carbon industry and the industry is being forced to reduce energy consumption to 50% by 2030 globally. In this context, How IBL is gearing up in providing an efficient solution to reduce the energy requirement?
The only way now paper mills can reduce their carbon foot print is by utilising Biomass and Cogeneration.
Q: With a vast pool of highly talented and experienced engineers, IBL has continued to maintain its reputation as a Research Powerhouse of Boilers, IBL’s research is 5 to 10 years ahead of time. What new technology or products on which IBL has been doing research, please elaborate.
IBL has been steadily increasing the efficiency of boilers for example can offer 99% efficiency in PNG boilers, +84% Efficiency in Coal fired and Bio mass boilers. It is well known that IBL group which was the part breaker for enabling small size paper mill to go in for cogeneration on an economical and commercial scale. Also IBL has the credit to successfully utilise difficult Bio mass on commercial scale like Rice straw (Parali), Mustard straw and many others including other waste.
Q: Small paper mills are also looking for efficient boilers on a reasonable budget, how IBL caters to their demand out of its product portfolio?
IBL has been offering highly efficient boilers with steam turbine even to the smaller paper mills below 50 TPD on a sustainable economic model.
Q: What are the various boilers IBL provides to the paper-making industry? How does IBL differentiate its various boilers in the context of various process applications? Please provide an example.
We provide different models as under.
• Agropakboilers (Saturated /Low pressure) in the range of 1000 – 30,000 Kg/Hr for 10 to 300 T/d paper plants with (PRT) steam turbines enabling incidental cogeneration of power. (Saturated boiler)
• Effigen-SD boilers (Mid-Range pressure about 24- 40 kg/cm²)in the range of 6000 – 30,000 Kg/Hr for 30 to 300 T/d paper plants of power. with steam turbines enabling cogeneration of power.
• Magnum and Magnogen (High pressure) boiler in the range of 6000 – 100,000 Kg/Hr for 100 to 1000 T/d paper plants.
of power. with steam turbines enabling cogeneration of power or power generation through condensing extraction steam turbines.
Q: What market size of heat & steam generation equipment do you see in India and Globally? What market growth do see in the next 10 years in this equipment category?
We expect a growth rate of around 15 to 20% every year in the heat and power sector in the paper industry.
Q: The Turbine segment is one of the very complexes in order to optimize the energy used and deliver maximum output at minimum fuel cost. Big players are gripping this market, how does IBL’s turbine technology be different and effective in comparison to other small and medium players?
IBL has expanded their portfolio in steam turbines and offers highly efficient turbines.
The range is as under.
• Pressure Reducing Turbine (PRT) 0 to 600 KW inlet pressure 10 Kg/Cm2 to 40 Kg/Cm2 with Back pressure from 1.5 to 21 Kg/Cm2
• Single stage machines from 500 to 1500 KW inlet pressure 21 Kg/Cm2 to 45 Kg/Cm2 with Back pressure from 1.5 to 21 Kg/Cm2
• Multistage stage impulse turbines from 750 to 3500 KW inlet pressure 45 Kg/Cm2 to 80 Kg/Cm2 with Back pressure from 1.5 to 8 Kg/Cm2.
• Multistage stage REACTION turbines from 1500 to 15000 KW inlet pressure 45 Kg/Cm2 to 80 Kg/Cm2 with Back pressure from 1.5 to 12 Kg/Cm2.
• Condensing – Extraction (REACTION turbines) from 2500 to 15000 KW inlet pressure 45 Kg/Cm2 to 80 Kg/Cm2 with Extraction pressure from 1.5 to 30 Kg/Cm2.
Web Title: IBL has the credit to successfully utilise difficult Bio mass on commercial scale like Rice straw (Parali), Mustard straw and other waste